




Cane Pickup
Most of my work at the moment involves working with cane. Cane is made by taking a chunk of color on a punty (long metal rod), heating it up and then encasing it in clear glass. When the right amount of clear glass has been added and heated correctly, it is attached to a 2nd punty (so there is now a punty at both ends) and the glass is pulled into a long thin strand. See the pulling cane page for details on how this works.
The picture to the right shows some completed cane. Those with a single solid colour were made using the process just described.
The cane that has the twisted patterns (the blue and green ones in the middle) are made by taking some of the single colored canes, reheating them, adding more clear glass and then pulling them again while quickly twisting the punties. This produces the spiral patterns. Thousands of different patterns are possible depending on how you set up the cane for this second pull. (And you could then take twisted cane and recombine that and pull it again - but at some point the color starts to fade as it is pulled thinner and thinner).
The piece is designed by deciding on the desired cane colours and pattered desired. The layout on the wood board to the right shows one design with two different types of twisty cane interspersed with clear cane. Each cane is about 5" long and they are arranged side by side to form a pattern that's about 7 or 8 inches long; this is called a rollup. A kiln shelf is heated and then the cane rollup is transferred to the heated plate and allowed to come up to temperature for a few minutes. A large metal fork (called a pastorale) is used to pick up the plate and insert it into the glory hole to get much hotter. When the cane just starts to melt, it is squished together forming a solid rectangle.
Glassblowers usually work in pairs or sometimes larger groups for bigger or more complex pieces. There are often times where you need more than two hands to perform an operation and it is also more fun to work together. One person is always the lead on a piece (called the gaffer), while the other people are assistance. Jeff is shown here assisting me with this rollup. Later in the day we'll reverse roles and I'll assist him with his pieces.
So, while Jeff is dealing with heating up the cane, I'm busy making up a "collar" of glass on a blowpipe. This is a ring of clear glass around the end of the pipe that needs to have the right circumference to roll exactly once along the base of the cane. We use a caliper tool called a pi divider to give us the right diameter for this, and being precise in this process is very important.

When Jeff has the cane at the right heat and properly squished together and when I have the collar constructed we bring the two together. The pastorale and plate are presented at the bench and I take the hot collar and literally roll the cane off the plate onto the collar. If everything goes just right, the two ends of the cane meet and a perfect tube of glass is formed. If the collar is a little to bit or too small, it gets more interesting….


The cane is then reheated in the glory hold, and then smoothed out on the marver. At this point I may also put a twist into the cane by putting a bit more pressure on the tip of the glass and frictioning it against the surface of the marver.
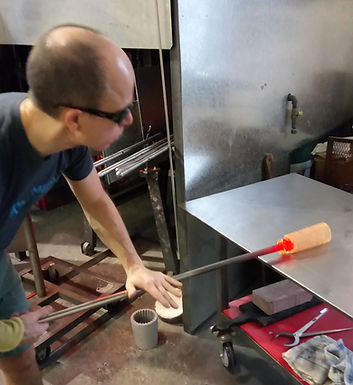
When the cane is reasonably smooth, the ends of the cane are pulled together using the jacks. The diamond shears finish crimping the end and the "flower" at the end is knocked off. This forms a closed tube of glass which is then reshaped slightly, allowed to cool a bit and then returned to the furnace to pick up another layer of glass.


From this point forward the glass can be blown in much the normal fashion to make the desired piece - a vase, bowl, plate or other form as desired. The difference is that the final piece will have the distinct lines or twisted patterns of the cane that was used at the start.
